Industrial Castings Densification
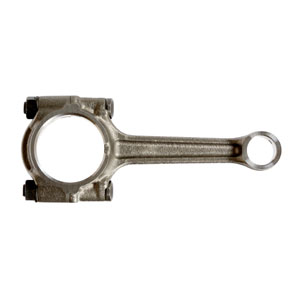
- Electrical, Electronics & Telecommunications Housings
- Machine Tools
- Water Industry Cast Impellers & Casings
Industrial applications for hot isostatic pressing (HIP) covers a wide range of industries and products. Aluminum precision castings for electrical, electronic and telecommunications equipment are HIPped to not only remove porosity and increase strength, but also to provide a smoother surface for improved sealing and finish application properties. HIPping removes porosity from sintered tungsten carbide tooling and in diamond tools improves the adhesion of diamonds to the base metal. In the water industry, cast impellers and casings for critical pumping applications are HIPped to improve integrity by eliminating porosity.
Advantages:
- HIP densified castings show improved strength, ductility and fatigue life with significantly less variation from casting to casting. The improved and more consistent material properties reduces part over design. This also decreases quality assurance costs and opens new applications.
- By removing service-induced porosity, HIP rejuvenates castings, extending their service life for improved economy.
- Hot isostatic pressing salvages castings scrapped for internal porosity - in fact, it is the only effective way to repair porous castings. Casting yield is significantly improved, resulting in lower costs and more effective utilization of raw materials.
- Significant cost savings may be realized by starting with a cast part and then HIPping to improve its properties as compared to machining the part from a solid.
Industrial materials that typically can be densified using HIP:
- Aluminum alloy castings
- Composites
- Cobalt chromium alloy castings
- Stainless steel castings
- Alloy steel castings
- Superalloy castings
- Titanium castings